- Amazon now has more than 1M robots in its facilities—nearly matching the number of human warehouse workers.
- Roughly 75% of Amazon’s deliveries are assisted by robotics, streamlining operations and reducing repetitive labor.
- While some jobs are being replaced, Amazon says it has retrained over 700K workers for higher-skilled roles in robotics and AI-assisted operations.
- Automation is helping Amazon cut workforce growth, increase productivity, and test next-generation warehouse robots—including humanoid prototypes.
Approaching The Automation Tipping Point
Amazon is rapidly approaching a historic milestone in warehouse automation: an equal number of robots and human workers, reports WSJ. The company recently announced it has deployed over 1M robots across its logistics facilities—the highest total to date—while employing about 1.56M people globally, most of whom work in warehouses.
This growing robot workforce is transforming Amazon’s fulfillment operations. Tasks like picking, sorting, and packaging are now often handled by robotic arms and autonomous mobile units.
Machines Taking The Load
Amazon’s robotic fleet includes Vulcan, a newer robot with tactile sensing that allows it to handle items from shelves, and mobile bots that move carts around fulfillment centers. About 75% of Amazon’s global deliveries now involve some form of robotic assistance.
For warehouse workers, the shift means fewer physically demanding tasks and more opportunities to operate or supervise automated systems. Former picker Neisha Cruz now remotely manages robots from an office, earning significantly more than she did on the warehouse floor.
Smaller Footprints, Bigger Gains
Amazon’s automation is driving major productivity gains. The company now ships about 3,870 packages per employee annually, up from 175 a decade ago. The average employee headcount per facility—670—is at its lowest in 16 years, reflecting how newer, robot-heavy buildings are designed to operate with fewer workers.
These advancements have helped Amazon slow hiring growth, while speeding up order fulfillment. At Amazon’s 3M SF Shreveport site, AI and robotic arms boost package processing speeds by 25% over older facilities.
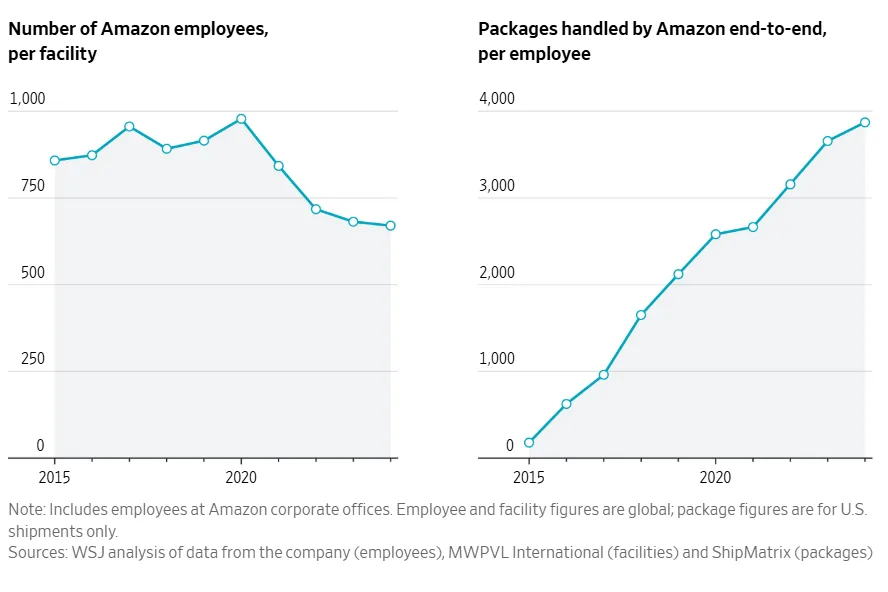
Training For The Future
Amazon has retrained more than 700K employees for roles involving robotics, AI, and mechatronics. The company is also investing in research teams to develop next-generation warehouse assistants that can respond to voice commands or handle complex tasks like unloading trailers.
Amazon is even testing humanoid robots developed by Agility Robotics, though these remain in R&D.
Amazon says automation complements human labor, not replaces it, despite ongoing concerns over potential job displacement in warehouse operations.
Why It Matters
Amazon’s shift toward a robot-heavy workforce reflects a broader trend in industrial automation. As one of the largest private employers in the US, its adoption of AI and robotics could reshape labor practices across the logistics and manufacturing sectors.
Automation eases labor challenges but sparks concerns about long-term job reductions in large-scale warehouse and fulfillment operations.
What’s Next
Amazon’s automation push is far from over. AI now boosts inventory and forecasting, enabling the company to reduce headcount while adding more tech-driven roles.
As robotics and AI advance, Amazon’s logistics model may serve as a global blueprint for supply chain automation.